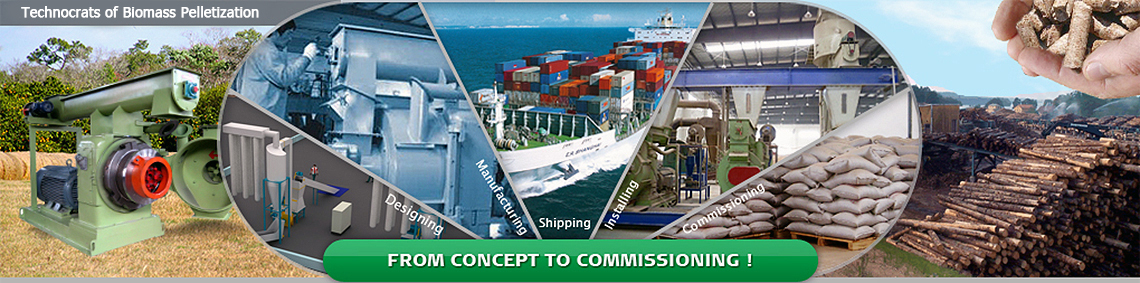
Make Your Sawdust Pellet Mill More Efficient
The granulation section is the most important part of the sawdust pellet mill, and the sawdust pellet mill is the most important part of the entire pellet production line. Whether the equipment is operating normally or the staff is operating properly will directly affect the quality and service life of the sawdust pellet mill. Gemco summarized many years of on-site management experience and theoretical knowledge, summed up the following points on how to properly use wood pellets machine: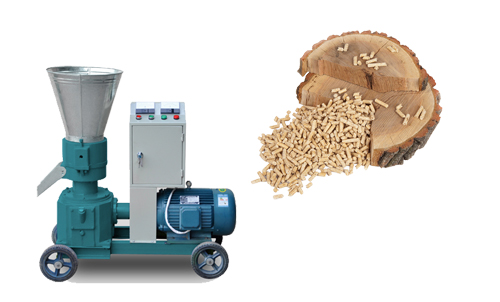
The raw material that enters the sawdust pellet mill must be powders. The particle size of the powder should have a certain size, and generally should be less than 2/3 of the diameter of the die hole. If you want to produce sawdust pellets with a diameter of 8mm, then the diameter of the raw material powder must be less than 6mm in order to increase production efficiency and yield.
The humidity of raw materials should be controlled between 15% and 18%. If the moisture of the raw material is even, the forming rate of the product pellets is higher, the yield is larger, and the density is higher.
The quality of the pellets and the level of production are closely related to the technical level of the workers in the pellet plant. They need to produce high-quality pellets based on changes in ambient temperature and humidity around the pellet plant's workshop. At the same time, they also need to pay attention to raw material moisture, dimensions, equipment wear, and special customer requirements. Workers in the pellet plant must have rich knowledge, rich experience, and a strong sense of responsibility in order to produce high quality, high-priced sawdust pellets.
Pay attention to the lubricating condition of the sawdust pellet mill. Bearings are required for the operation of any equipment. The bearing must work under lube conditions. Once the lubricant is low, the bearing burns out and the machine stops. Therefore, the lubrication of the sawdust pellet mill plays an important role in the production efficiency and quality of the sawdust pellet mill.
Take care of wearing parts. The mold and pressure roller are wearing parts of the granulator. Increasing the useful life of wearing parts means saving costs and increasing profits. The selection of raw materials must be strictly in accordance with the requirements of customers to ensure the cleanliness of raw materials. Prior to the start of pelletizing, screening equipment and strong magnetic blocks were added to reduce the damage caused by large pieces of wood to the die and pressure roller.
In order to make the sawdust pellet mill more productive, better quality, and low failure rate, it requires the operator of the pellet plant to study the performance of the pelletizing equipment. Only in this way, sawdust pellet mills can produce pellets better.
Features of GEMCO sawdust pellet mill
- The granulator is made of high-quality materials and the supplier of its electrical components is the famous brand Siemens.
- Our rollers and dies have a longer life than ordinary rollers and dies. The flat die can be used on both sides to extend its service life.
- Flat die pellet mill is small in size. It occupies less space than a ring die pellet mill and does not require a large workshop to operate.
- Suitable to process a wide range of biomass raw material.
- We also provide 24/7 service for our customer, we have a professional pre-sale and after-sale service team.