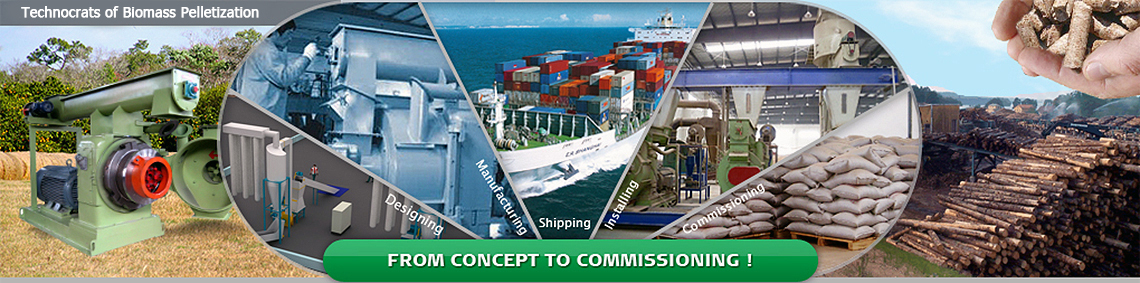
What Kind of Role the Pellet Die Plays in a Pellet Mill
The pellet die is the core part of a pellet mill. The quality of the pellet die will directly influence the performance of the pellet mill. Or we can say that the output of a pellet mill is determined by its pellet die. So, it is wise to check the quality of the pellet mill die before you are to purchase a pellet mill.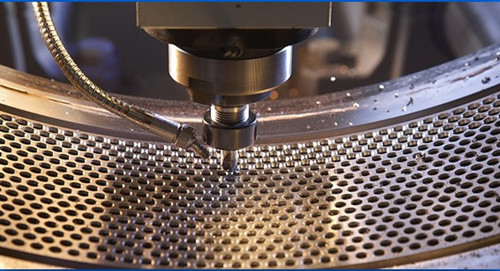
How to judge the quality of a pellet die?
The surface of the pellet die.
A high-quality pellet die should have a smooth surface. The CNC machining center is the technical support for advanced pellet dies. The pellet dies produced by the CNC machining center have a good surface finish, uniform tool texture, and a smooth surface. Some manufacturers use ordinary machine tools to save costs. Their pellet dies are not as smooth as CNC machining center’s and have a rough surface.The shape of the pellet die
High-quality pellet dies have consistent dimensions. CNC machining centers produce pellet dies with high precision and consistent dimensions. This high degree of accuracy and dimensional consistency is not achievable by conventional machine tools. The consistency of the die ensures uniform pelletizing pressure and interchangeability of all pellet dies, making it easier for users to repair and replace dies.The hardness of the pellet die
High-quality pellet dies are made of high-quality alloy steel that has been specially heat treated. The Rockwell hardness of this steel can reach 60 degrees. All kinds of processing tools, including drills and taps, can not cause any damage to the pellet made of this steel, so straw and other biomass materials are difficult to damage it. The hardness of ordinary carbon steel made pellet die is only 45 to 50 degrees, sharp hard tools will damage it, greatly reducing its wear resistance.The tenacity of the pellet die.
The steel being used to process high quality pellet die have been repeated forging, which makes the molecular arrangement more compact. The compact of molecular arrangement has strengthen the toughness of pellet die and makes it 2 to 3 times more tough than ordinary carbon steel plate, ensures the pellet die in long-term high strength state without deformation.The steel used to process high quality pellet dies needs to be forged repeatedly to make it more compact. The compact molecular arrangement enhances the toughness of the pellet die, making it 2 to 3 times more flexible than ordinary carbon steel plates, ensuring that the die will not deform even under long-term, high-strength use.
Characteristics of GEMCO pellet mill pellet dies:
- Superior material. GEMCO pellet die adopts high strength alloy, making the products firm and reliable.
- A lot of experimentation. Every machine we produce must undergo trial and error before we can play. We strive to make progress in the machinery manufacturing industry. Our technical team is always looking for new breakthroughs. Collaborate with front-line employees and combine customer feedback to continuously experiment and improve.
- Support of high tech machinery. Electrification operation, Computer manipulation. The thickness of dies are uniform, surfaces are smooth, the sizes of the die holes are unified and arranged in order. There will be no skew hole, block hole or overlapping hole, etc.
- High-tech mechanical support. We use computer operation to achieve automated production. The pellet dies we produce are uniform in thickness, smooth in surface, uniform in size, and arranged in an orderly manner, and are not provided with inclined holes, closed holes or overlapping holes.
- Long service life. Both sides of GEMCO pellet die can put into use. Its service life can reach 800 hours if used properly.
- Die hole size can be customized. You can customize the most suitable die hole according to your raw material needs. We can provide you with raw material testing, if you need, please contact our customer service center, our staff is ready to help.
- Good after-sales service. If you need to replace a new mold, the new mold produced by the original factory is your best choice. The rollers and dies should be replaced at the same time so that any old or damaged will cause no damage to the other, or affect the production of pellets. At the same time we also provide other spare parts.