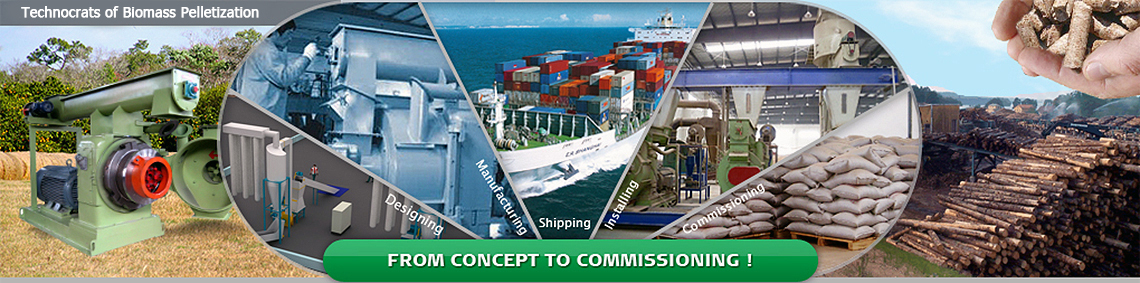
Factors may Affect the Hardness of Feed Pellets
The hardness of feed pellets can be affected and determined by many factors. It is important to know them in the feed pellets production.
Effect of pulverization process on pellet hardness
The particle size of the raw material is the decisive factor to the pellets’ hardness in the comminution process. Generally speaking, the finer the crushing granularity of raw materials, the easier the starch gelatinization in the process of conditioning, the stronger the bonding effect in granular materials, the less easy the granules to break, and the greater the hardness.
Expansion process of raw materials on pellet hardness
By puffing and expanding the raw material, we can destroy the anti-nutritional factors, remove toxins, kill bacteria, eliminate harmful substances, denaturate protein and gelatinize starch. The effect of gelatinized starch on pellets’ hardness is significant. Since the expanded pellets have a large degree of gelatinization of the starch, the hardness of the pellets is also large.
Effect of steam quenching and tempering process on pellet hardness
Steam quenching and tempering is the key link in the processing of feed pellet. The effect of quenching and tempering directly affects the internal structure and appearance quality of the pellet. Steam quality and quenching and tempering time are two important factors affecting the quality of quenching and tempering. High quality dry saturated steam can provide more heat to improve the temperature of material and make starch gelatinized. The longer the tempering time, the higher the gelatinization degree of starch, the denser the granular structure, the better the stability and the harder the formed starch is.
Effect of pellet mill die on pellet hardness
The technical parameters such as the diameter and compression ratio of the ring die of the granulator can significantly affect the hardness of the pellets. The hardness of pellets made by ring die with the same aperture and different compression ratio increases with the increase of compression ratio. Selecting suitable compression ratio ring die can produce pellets with good hardness.
The length of the pellets has a significant effect on their pressure bearing capacity. For pellets of the same diameter, the longer their length, the greater the hardness measured if the pellets are free of defects. Adjust the position of the cutter in the pellet mill to ensure the proper pellet length, so that the hardness of the pellets remains basically the same.
The section shape of particle diameter also has a certain influence on the hardness of particles. The 8-shaped section has a stronger compressive capacity than the circular section, and the pellet hardness measured is also larger.
In addition, the material of the ring die has a certain effect on the appearance and hardness of the pellets. The pellets produced by ordinary steel ring die and stainless steel ring die is quite different.
Effect of drying and cooling process on pellet hardness
In order to ensure the quality of the product within a certain period of time, the feed pellets made by the pellet mill need to be dried and cooled. In the experiment of measuring particle hardness, after cooling the same product for 5 minutes, 10 minutes and 15 minutes, it was found that the hardness of particles with low hardness was not significantly affected by cooling time, while the hardness of particles with larger hardness decreased with the increase of cooling time.
This may be because the brittleness of the particles increases with the loss of water in the particles, thus affecting the hardness of the particles.
In the feed pellet processing, the factors affecting the hardness of pellets are far more than these. With the in-depth study of more and more scientists and technicians who are keen on the technology of feed processing, more and more methods of controlling the hardness of pellets will be mastered by people. I believe that in the near future, we can produce various kinds of animal-friendly feed pellets.